ウェハ加工におけるスライシングの役割と基礎知識
ウェハのスライシング工程は、半導体ウェハ製造において最も初期の段階であり、ウェハの厚みや表面品質を決定する重要な要素です。本章では、スライシングの基本的な役割や主要な技術、そして精度やコストへの影響について解説します。
ウェハ加工全体の流れとスライシングの位置付け
ウェハの製造工程において、スライシングは最初の重要なステップです。インゴットからウェハを切り出すこのプロセスは、後続の研磨や洗浄工程の効率や品質に大きく影響します。スライシングの精度が低いと、ウェハの厚みのばらつきが生じ、後工程での歩留まり低下やコスト増加につながります。
スライシング技術の種類と特性
スライシング技術には様々な手法がありますが、以下に例を示します。
・遊離砥粒方式
スラリー(研磨剤を含む液体)を用いて切断する方法。切削力は比較的弱いが、表面のダメージが少ない。
(例)スラリーを用いたワイヤスライス
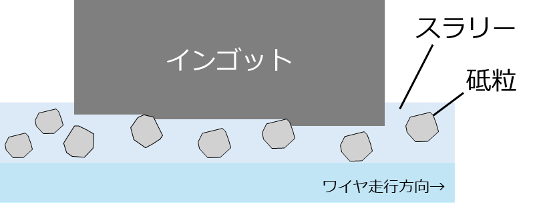
・固定砥粒方式
ワイヤやブレードに砥粒を固定して切断する方法。切削速度が速く、比較的精度が高い。
(例)ダイヤモンドワイヤによるスライス、内周切断機
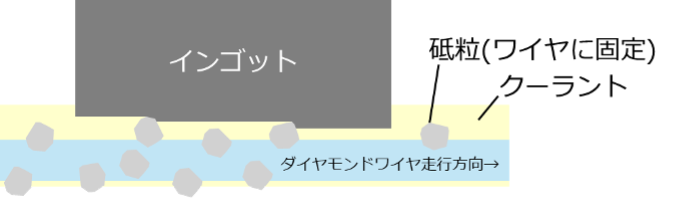
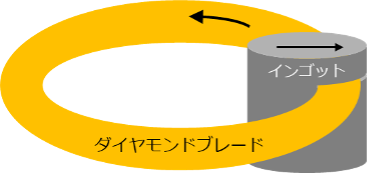
・非接触加工方式
電気やレーザーを利用してウェハを切断する方法。機械的ストレスがないが、熱影響が発生する可能性がある。
(例)放電加工、レーザースライス
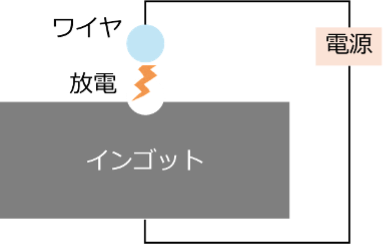

スライシングの精度と製造コストへの影響
スライシングの精度は、ウェハの品質や生産コストに大きく関与します。例えば、スライス時に生じるカーフロス(※1)は、材料ロスの要因となります。高精度なスライシング技術を用いることで、カーフロスを最小限に抑え、コスト削減と歩留まり向上が可能になります。
(※1)切断時に切削粉として除去される個所。切り代。
ウェハ加工におけるスライシングの課題とその影響
ウェハスライシングでは、カーフロスやマイクロクラックといった課題が存在し、これらが生産コストや後工程の歩留まりに影響を与えます。本章では、それらの課題を取り上げ、解決に向けたアプローチや必要な技術について説明します。
課題①:カーフロス
カーフロスは、ワイヤの太さや加工方法に大きく依存し、スライシング工程における材料ロスの主な要因となります。特に、従来のスライシング技術では、ワイヤの直径が大きいほど加工速度を向上させられる一方で、カーフ幅が広がり、結果として材料の無駄が増えるという課題があります。そのため、ワイヤ径を細くすることでカーフロスを低減する手法が広く検討されていますが、ワイヤ径を小さくすると、切削時の剛性が低下し、ワイヤの振れや断線のリスクが高まるという問題が発生します。また、ワイヤとウェハの接触面積が減ることで、切削速度が低下し、生産性が落ちるというトレードオフも生じます。
課題②:マイクロクラック
スライシング後のウェハには、目に見えない微細なクラック(マイクロクラック)が発生することがあり、これがウェハの品質に深刻な影響を与えることがあります。マイクロクラックは、主にスライシング時に発生する機械的応力や熱影響によって形成され、肉眼では確認できないものの、後工程の洗浄、エッチング、研磨などの処理を経る中で拡大する可能性があるため、最終的な製品の歩留まりや信頼性を大きく左右します。特に、半導体や太陽電池用ウェハのような高品質が求められる分野では、マイクロクラックの管理が極めて重要となります。
課題③:反り(ワープ)
前述の遊離砥粒方式や固定砥粒方式を採用したワイヤソー方式による半導体結晶インゴットのスライシングは、直径300mm、長さ500mm程度のシリコン単結晶インゴットの切断に多く適用されています。このような大口径、長尺、大重量インゴットのワイヤソーによるスライシングでは、切断熱によるインゴットの熱変形やワイヤーガイドローラーの熱変形、及び切断装置の機械的な変形等が原因となって、インゴット直径と同程度の周期でウェハの切断形状が変化する、いわゆるウェハの反り(ワープ)を発生させることがあります。反りが発生すると、これを矯正するために後の研削加工や研磨工程に時間がかかり、コストアップの原因となります。そのため、半導体シリコンウェハの製造においては、スライシング工程にてインゴットから反りが抑制された真直ぐで平坦なウェハをスライスする技術の開発が非常に重要となっています。
課題④:ナノトポグラフィ
シリコン単結晶インゴットのスライシングにおいては、前述の反りとは対照的に短い数mmから数十mmの周期で微小なうねり(ナノトポグラフィ)が発生することがあります。ナノトポグラフィの発生原因には様々な要因がありますが、例えば、切断装置の一部であるインゴットの設置テーブルの機械的な取り付け精度などが影響していると考えられています。このナノトポグラフィは、電子デバイスから要求されるウェハの平坦度の一種であるSFQR(Site Front least sQuare Range)に影響をすると考えられています。従って、半導体シリコンウェハの製造においては、反り(ワープ)からナノトポグラフィまで、さまざまなスケールで変化するウェハの切断形状を精密に制御しながら加工する技術の開発が進められています。
ウェハスライシングを最適化するためのAI・機械学習活用
近年、経験や暗黙知から脱却した、AIや機械学習を活用したスライシングの条件最適化が進んでいます。スライシング工程における統計学的手法からニューラルネットワーク、深層転移学習といったAIを活用した手法を取り上げ、それぞれの利点と活用事例を紹介します。
ワイヤ放電加工によるシリコンウェハ切断の多目的最適化
統計学的手法を活用することで、スライシング条件を最適化する研究が進んでいます。例えば、Dongreらは応答曲面法(RSM)を用いて、図6に示すようなワイヤ径、ワーク高さ、電流、デューティ比(※2)などのプロセスパラメータを統計的に解析し、カーフロスの最小化とスライシング速度の向上を両立する最適条件を導出しました。その結果、従来のワイヤソーによるスライシングで約250μmだったカーフロスの幅を、最適条件(ワイヤ径40μm、ワーク高さ75mm、電流5A、デューティ比52.42%)で60.87μmに低減し、約76%の削減を達成しました1。また、微細なマイクロクラックを抑えた高品質なウェハの製造が可能であり、太陽電池や半導体用途に適用可能な技術として期待されています。
(※2)パルスOn⇔Off 1サイクルにおけるパルスOnの時間の割合(Ton / (Ton + Toff))。連続放電すると放電ギャップ内に溶融物や異物が蓄積し、加工精度が低下することがあるため。
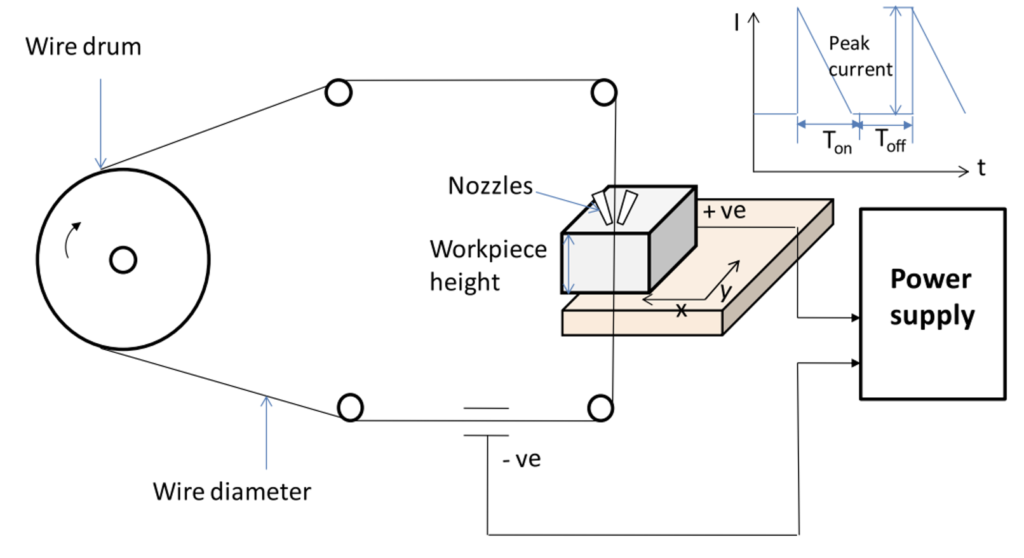
ニューラルネットワークを用いたシリコンウェハスライシングのプロセス最適化
Kayabasiらは、人工ニューラルネットワーク(ANN:Artificial Neural Network)を用いて、ダイヤモンドワイヤソーによるシリコンウェハスライシングのプロセスパラメータを最適化し、表面粗さ(Ra)の予測精度を向上させる研究を行いました2。28種類のスライシング条件で実験を実施し、ワイヤ速度、Z軸速度、クーラント比率がRaに与える影響を解析しました。その結果、ANNを用いることで99%以上の高精度な予測が可能となり、最適なパラメータ設定によって表面粗さを最小限に抑えつつ加工時間を短縮できることを示しました。これにより、今まで以上に効率的なウェハ製造プロセスの実現が期待されます。
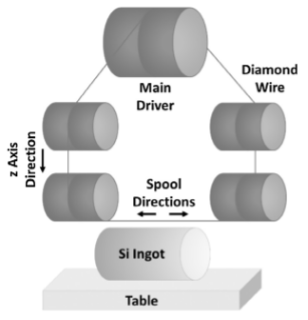
深層転移学習を活用した欠陥検出モデル
スライシング後のウェハに発生する欠陥を高精度に検出するために、深層転移学習を活用したモデルが開発されています。例えばGanumらは、深層転移学習を活用し、シリコンウェハの欠陥分類の精度向上を目指した研究を行いました3。特に、MobileNetV2 をベースモデルとして使用し、ウェハの欠陥画像データを追加学習させることで、高精度な分類モデルを構築しました。その結果、彼らの実験では6種類の欠陥(クラック、ダブルコントラスト、ホール、マイクロクラック、ソーマーク、汚れ)を対象に98.99%の分類精度を達成しました。この研究は、半導体製造におけるリアルタイム品質検査の自動化に寄与し、従来の目視検査や自動光学検査の精度を上回る可能性を示しています。
ウェハ加工におけるプロセスインフォマティクス
プロセスインフォマティクスは、データ駆動型のアプローチによって製造プロセスを最適化する手法です。データに基づいて製造プロセスを管理することで、品質向上やコスト削減が可能となり、製造業全体の効率化を支えています。
プロセスインフォマティクスとは何か
プロセスインフォマティクスについて詳細に説明したテックブログもありますので、そちらもご覧ください!
ウェハ加工とプロセスインフォマティクスにおける今後の展望
従来、スライシング工程の改善は個別最適が中心でしたが、近年では全工程を統合的に最適化するアプローチが求められています。例えばスライシングの精度を向上させても、後続の研削や研磨工程がボトルネックになることがあります。そのため単独の工程最適化ではなく、プロセス全体のデータを統合して最適化することが望ましいと考えられます。我々はこの課題に対し、プロセスインフォマティクスを活用することで、従来の手法では困難だった最適化を可能にしています。
アイクリスタルはプロセスインフォマティクスのプロフェッショナル集団です。当社の技術やソリューションに関心をお持ちの方は、ぜひ当社のホームページで詳細をご確認ください。
製造業におけるPIの最適なパートナーとして、皆様のご期待に応えます。
お問い合わせはこちら:お問い合わせフォーム
お気軽にご連絡ください。
参考文献
- Multi-objective optimization for silicon wafer slicing using wire-EDM process, Ganesh Dongre、Sagar Zaware、Uday Dabade、Suhas S. Joshi, Materials Science in Semiconductor Processing Volume 39(2015), https://www.sciencedirect.com/science/article/pii/S1369800115004667 ↩︎
- Determination of cutting parameters for silicon wafer with a Diamond Wire Saw using an artificial neural network, Erhan Kayabasi、Savas Ozturk、Erdal Celik、Huseyin Kurt, Solar Energy Volume 149(2027), https://www.sciencedirect.com/science/article/pii/S0038092X17303067 ↩︎
- Detection of Monocrystalline Silicon Wafer Defects Using Deep Transfer Learning, Adriana Ganum、D. N. F. Awang Iskandar、Lim Phei Chin、Ahmad Hadinata Fauzi, Journal of Telecommunications and Information Technology(2022), https://jtit.pl/jtit/article/view/431/43 ↩︎