樹脂成形は現代の製造業において欠かせないプロセスであり、AI技術の進化によりさらなる製造プロセス効率化と品質向上が期待されています。現在、新たなアプローチとして、AIと機械学習を製造プロセスに活用することで、従来の方法では難しかった最適化や効率化が可能となり、製造プロセス全体のパフォーマンス向上が期待されています。
本記事では、樹脂成形の基礎からAIによるプロセスの最適化までを解説し、高度な製造技術と最新の機械学習の応用例を解説します。
樹脂成形とは | 基礎知識と重要性
樹脂成形の基本概念と主要技術
樹脂成形とは、樹脂(プラスチック)を溶かして金型に流し込み、冷却して製品を製造する成形方法です。樹脂成形プロセスでは、多くの場合、材料をスクリューと呼ばれる混錬装置を使って溶融させ、スクリューが回転することで樹脂を押出または射出して成形します。このスクリューの使用の有無によって、樹脂成形方法を分類することが可能です
スクリューを用いる方法としては、押出成形、ブロー成形、射出成形などがありますが、射出成形は、特に自動車部品など多様な用途で最も広く利用されており、高い精度と生産性が求められる場面で重宝されています。
射出成形品の製造方法
射出成形品は、以下の流れで製造します。
- 金型を射出成形機にセットします。
- ホッパーから樹脂ペレットを供給し、スクリューを用いて樹脂を加熱・溶融させます。
- 溶けた樹脂を金型の射出口から高速かつ高圧で射出し、金型内に均一に充填します。
- 取り出しロボットなどを用いて、凝固した製品を金型から取り出します。
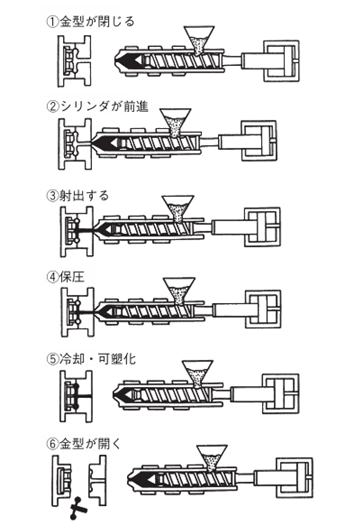
樹脂成形の用途と重要性
樹脂成形は、以下のような多様な用途で利用されています。
- 自動車産業:バンパー、内装部品などの製造など。特に軽量化用途では、従来の金属素材から樹脂への置き換えが進んでいます。
- 電子機器:スマートフォンケース、パソコン部品、家電筐体など。高精度な成形技術により、複雑なデザインや薄型化を実現します。
- 医療機器:注射器、カテーテル、診断機器の部品。樹脂成形により、耐久性の高い製品が大量生産されています。
- 日用品:ボトル、容器、家具部品など。多様なデザインを実現可能で、消費者のニーズに柔軟に対応しています。
樹脂成形は、軽量化、高精度、高い生産性により、製品のコスト削減と性能向上に大きく寄与しています。特に自動車の軽量化用途においては、従来の金属素材から樹脂への材料置き換えが進んでおり、これに伴う加工方法の革新も進展しています。これにより、燃費の向上や環境負荷の低減が期待されており、今後も技術革新が期待されています。
樹脂成形プロセスでよくある課題
材料特性の変動による品質の不安定さ
樹脂成形では、温度や湿度、樹脂の混合状態といった原材料の特性変動が製品の寸法精度や表面仕上がりに影響を与えます。特にリサイクル材やガラス繊維(GF)強化材を使用すると、品質への影響が顕著になります。リサイクル材では、不純物の混入や水分含有量の変動により、成形品に表面欠陥や気泡、割れが発生しやすく、機械的特性も低下します。このような特性変動により品質の制御が困難となるため、安定した特性を持つ樹脂材料が一般的に使用され、リサイクル材の利用拡大が進まない問題があります。
さらに、繊維配向の変動も品質に大きな影響を及ぼします。繊維の配向が不均一だと、機械的特性にばらつきが生じ、寸法安定性が低下します。これに対処するために、CAEツールを用いて成形プロセス中の繊維配向を予測し、製品の使用条件下での応力分布を解析することで、必要な強度を確保するために樹脂流れを調整する方法が一般的に採用されています。
まとめると、樹脂成形における原材料および繊維配向の特性変動は製品品質に重大な影響を与えるため、これらの変動を予測・制御する技術の活用が求められています。また、リサイクル材の特性変動が品質管理を困難にし、利用拡大の障壁となっている現状があります。
金型設計とプロセス条件の最適化の難しさ
樹脂成形における金型設計とプロセス条件の最適化は、製品の品質向上や生産効率の向上に直結する重要な課題です。金型設計時には、樹脂の流動性や充填バランス、冷却効率など、多岐にわたる要素を考慮しなければなりません。特に、複雑な形状や薄肉部品の成形では、樹脂が均一に流れるよう設計することが求められ、ムラや欠陥を防ぐための緻密な設計が必要です。
また、金型設計時には数値シミュレーションやモデリングを用いて最適化を図ることが一般的ですが、シミュレーション結果と実際の成形結果を一致させることは難しく、現場での微調整が必要となります。
さらに、樹脂の熱特性や流動特性、収縮率などは材料ごとに異なるため、特性に合わせた金型設計やプロセス条件を設定する必要があります。また、金型を製作するためには高額な初期投資が必要であり、試作や修正を繰り返すことでコストと時間が大幅に増加するリスクも伴います。このため、金型設計前にデジタルツイン上での最適化が求められます。
プロセス条件もまた、成形温度、圧力、射出速度、冷却時間などが互いに影響し合うため、これらの条件を適切に設定しないと、収縮や反り、気泡、ショートショットといった成形欠陥が発生しやすくなり、製品の品質低下や歩留まりの悪化を招きます。
以上のように、樹脂成形における金型設計とプロセス条件の最適化は、多岐にわたる要素をバランス良く調整するための高度な技術と職人の経験が必要とされてきました。
不良品率低減に向けた現状の限界
樹脂成形における不良品率の削減には、いくつかの重要な課題が存在します。まず、使用する樹脂材料は種類が豊富でそれぞれ異なる特性を持ち、材料ロット間の変動が品質に影響を与えます。
さらに、成形プロセス中の温度、圧力、射出速度などのパラメータをリアルタイムで正確に制御・監視することはとても難しく、これが不良品の発生につながります。また、数値シミュレーションと実際の成形結果との間にギャップが生じることや、オペレーターの技術や経験に依存する人的要因も不良品率の低減を妨げています。
加えて、製造環境の温度、湿度などの環境要因も成形品質に影響を与えます。さらに、環境規制の強化や持続可能性への要求が高まる中で、リサイクル材料の使用やエネルギー効率の向上といったプロセス変更が必要となり、これが一時的に不良品率の増加を招く可能性もあります。
樹脂成形プロセスにおける最適化事例
樹脂成形の製造プロセスには、上記のように多くの課題があります。しかし、AIと機械学習の技術を製造プロセスに適用するという新たなアプローチを導入することで、これらのプロセスの効率化と品質向上が期待されています。ここでは、樹脂成形プロセスにおける最適化事例をご紹介いたします。
機械学習を用いた射出成形の品質管理の自動化
製造業における品質管理(QC)は特に射出成形のような大量生産技術において不可欠ですが、従来の人による検査や統計的プロセス制御(SPC)は時間とコストがかかり、検出精度にも限界がありました。そこで、機械学習(ML)を活用した自動化QCシステムの開発が進められています。Stevenら[2]は、冷却水温度、溶融温度、流量、圧縮圧力、粘度モデルの指数n、Cross-WLFモデルのD1定数などの入力パラメータを変動させたシミュレーションデータを用いて、Light Gradient Boosting Machine(LGBM)による樹脂成形品寸法の良品・不良品分類モデルを開発しました。開発したモデルは、Accuracy 99.4%、Specificity 99.7%、Sensitivity 94.7%という高い予測性能を達成し、射出成形品の品質管理を大幅に改善できる可能性を示しました。今後は実データへの適用とモデルの最適化を進めることで、製造業の品質管理の効率化とコスト削減に寄与することが期待されます。
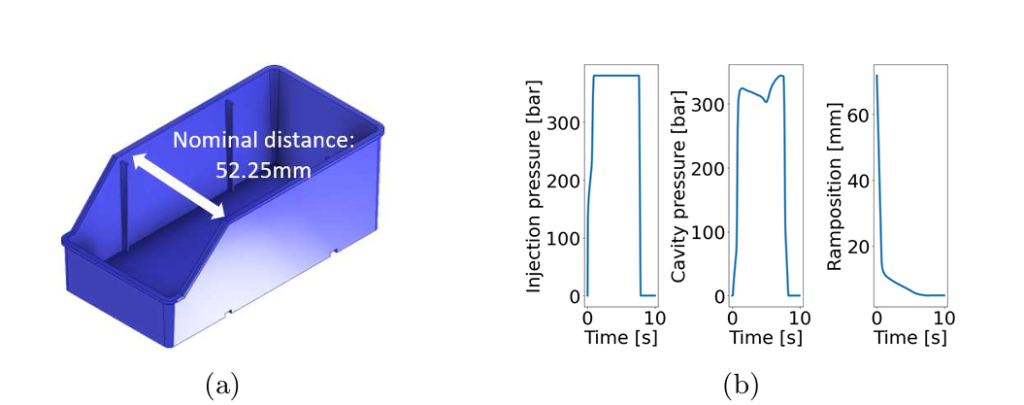
In-LINEな品質管理とリアルタイム制御
Saeidら[3]は、Industry 4.0に準拠した完全自動化されたクローズドループ射出成形システムを提案しています。
このシステムの主な特徴は以下の通りです:
- インライン測定:重量、寸法特性、表面品質といった主要な品質指標を自動で測定。
- データ収集と分析:OPC UA通信プロトコルを使用して、射出成形機や周辺機器からのデータをリアルタイムで収集・分析。
AI制御システム:収集したデータを基に、ResNet-18などの深層学習モデルを用いて品質を予測し、MPC(モデル予測制御)アルゴリズムを通じて新しい機械パラメータを設定。
本研究では、ABS樹脂成形品の重量予測においてR²スコアが98%以上という非常に高い精度を達成し、AIを活用したプラスチック射出成形プロセスにおけるインライン品質管理システムの有効性を実証しました。製造業におけるデジタルトランスフォーメーションの一環として、今後もこうした技術の進化が期待されます。
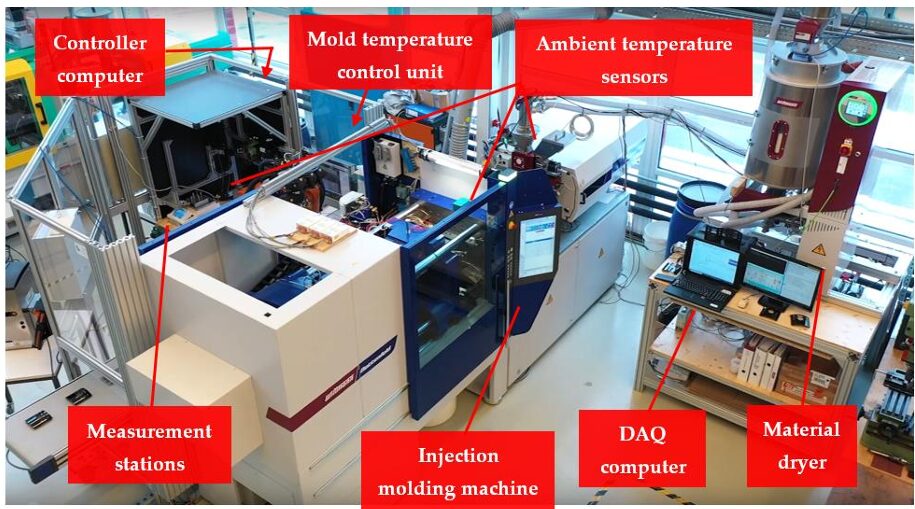
射出成形CAEにおけるAIの活用
AI技術を活用した歯車成形品の収縮率予測に関する事例が報告されています4。まず、歯車の収縮率に関するCAE計算結果と実測データを収集し、3D CADデータから体積や表面積などの特徴量を抽出して製品形状を数値化します。これらの特徴量に成形条件や樹脂データを加え、解析結果と実測値の誤差を出力とするニューラルネットワークを訓練しました。
この学習済みモデルを用いれば、新しい製品データに対して最適な解析パラメータが予測でき、さらに遺伝的アルゴリズムを使った逆問題の解法によって、最適な成形パラメータを導き出せます。従来は金型修正や成形実験に約1年を要していたプロセスが、この手法により約2日で同等の成果を得られるようになりました。
精度については、従来手法では誤差率を22%から12%に改善できていたところが、AIの導入後は6%にまで低減。データの分散も1/3以下に抑えられ、解析の安定性と信頼性が大幅に向上しました。
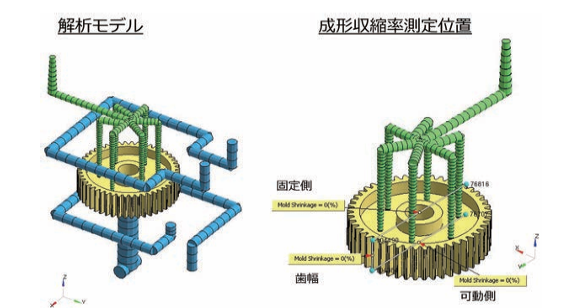
プロセスインフォマティクスが実現する樹脂成形の未来
プロセスインフォマティクスが樹脂成形技術にどんな変化をもたらすのか、今後の展望について考えていきます。
プロセスインフォマティクスの導入における付加価値
プロセスインフォマティクスは、製造プロセスに関するデータを解析し最適化を行う技術です。データに基づいて製造プロセスを管理することで、品質向上やコスト削減が可能となり、製造業全体の効率化を支えています。
プロセスインフォマティクスについては本テックブログにてとても詳しく解説しておりますので、ご覧ください。
プロセスインフォマティクスを用いることで、成形プロセス中に収集される大量のデータ(温度、圧力、速度など)を解析し、製品の品質をリアルタイムで予測することができます。例えば、温度変動が原因で発生する寸法不良を早期に検出し、即座にパラメータを調整することで、不良品の発生を大幅に削減できます。
樹脂成形では、加熱や射出、冷却などさまざまな工程がありますが、プロセスインフォマティクスを使って最適な条件を割り出すことで、材料のムダを減らし、エネルギー消費を抑えつつ、生産スピードを上げることができます。たとえば、冷却時間をうまく調整すると、サイクルタイムが短くなり、生産ライン全体の効率が高まります。
AI技術との融合による製造業の変革
AI技術が製造業に取り入れられると、製造業全体の競争力が高まるだけでなく、環境に配慮した生産体制づくりにもつながります。なかでも樹脂成形の分野では、AIの導入で製品の品質を上げたり、生産効率を大きく向上させたりできるため、これからさらに注目されるでしょう。製造業とAIを組み合わせる取り組みは、これからのものづくりを形づくる大きなカギとなり、持続的な成長と新たな革新を生み出す土台になっていくでしょう。
アイクリスタルはプロセスインフォマティクスのプロフェッショナル集団です。当社の技術やソリューションに関心をお持ちの方は、ぜひ当社のホームページで詳細をご確認ください。
製造業におけるPIの最適なパートナーとして、皆様のご期待に応えます。
お問い合わせはこちら:お問い合わせフォーム
お気軽にご連絡ください。
参考文献
- 青葉 堯. (2010). 本当によくわかる 射出成形金型設計入門. 日刊工業新聞社. ↩︎
- Steven Michiels, Cédric De Schryver, Lynn Houthuys, Frederik Vogeler, Frederik Desplentere, “Machine learning for automated quality control in injection moulding manufacturing,” ESANN conference proceedings, 2022. ↩︎
- Saeid Saeidi Aminabadi, Paul Tabatabai, Alexander Steiner, Dieter Paul Gruber, Walter Friesenbichler, Christoph Habersohn, Gerald Berger-Weber, “Industry 4.0 In-Line AI Quality Control of Plastic Injection Molded Parts,” Polymers, 2022. ↩︎
- 山田高光, “射出成形CAEにおけるAI技術の応用”, 成形加工 第32巻第3号 2020. ↩︎