レーザー加工技術とは、レーザーポインターなどで知られる指向性を持った光の特性を産業用途へ応用した技術を指します。その応用先は、切断や溶接をはじめ、表面処理や精密加工、微細構造の形成など多岐にわたります。中でもレーザー溶接は、金属などの加工対象を溶融・凝固させることで部材の接合を達成する溶接工法にレーザーを適用させた技術であり、非接触で高速かつ高精度な加工が可能な点で、生産性向上に大きく貢献する次世代工法として注目を集めています。また、レーザー溶接は光を利用する性質上、各種センシング設備との連携がしやすく、加工プロセス中のモニタリング技術開発も盛んにおこなわれています。このため、近年注目されるAIや機械学習と組み合わせることで、従来の溶接手法では実現が難しかった最適化や効率化による製造プロセス全体のパフォーマンス向上への期待も集めています。本記事では、レーザー加工技術の中でも特にレーザー溶接にフォーカスし、技術の基礎から最新のプロセスインフォマティクスの検討事例をご紹介します。
レーザー溶接の基礎知識と最新技術
レーザー加工技術の分類とレーザー光源
レーザー加工はFig.1に示すように、切断、溶接、焼き入れなど多岐にわたります。このレーザー加工に用いられるレーザー光は、日常で目にするレーザーポインターと同じ発振原理を基本としながらも様々な種類が存在します。そのため、Table.1ように加工目的や加工対象の材質、厚みなどに対し、波長、発振形態、最大出力などの特性が最適となるレーザー光源を選択することも重要なポイントとなります。たとえば、レーザー溶接分野においては、安定した高出力と高いビーム品質を実現するファイバーレーザーが主流となっており、精密なエネルギー制御によって均一な溶接が可能となっています。また、半導体レーザーは変換効率の高さや波長選択性の観点で近年注目を集めています。
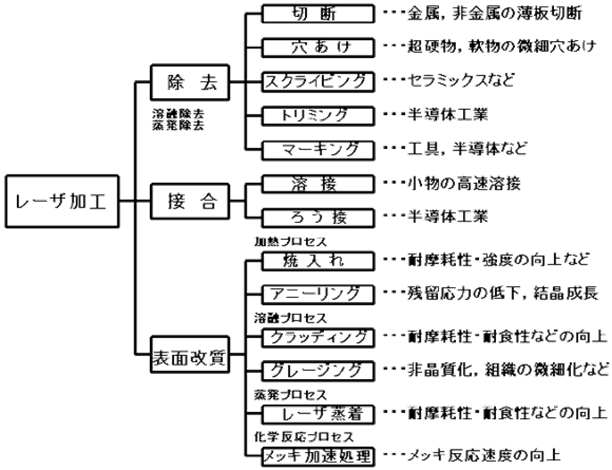
Fig.1 レーザー加工の分類1
Table.1 加工用レーザー光源の種類2
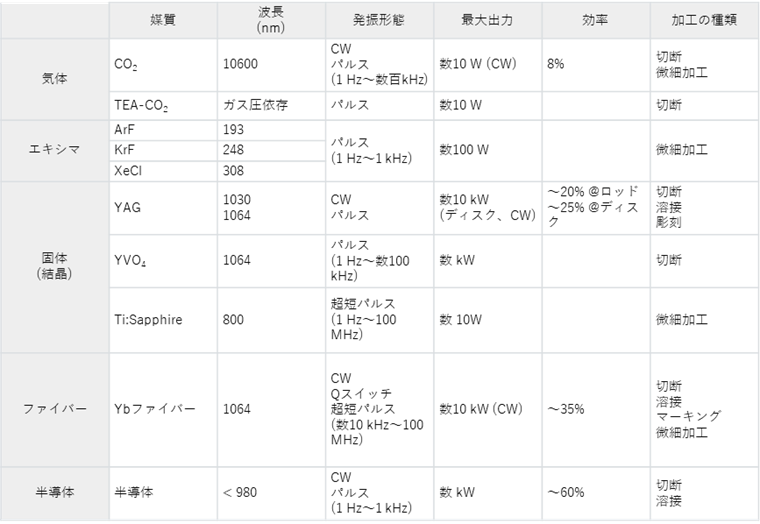
レーザー溶接の特徴
ここではレーザー溶接の特徴を大きく2点紹介します。まず一つ目は局所加工です。レーザー光を数十~数百μm程度の狭い範囲に集中して照射することで、局所的・急激な温度上昇および溶融を実現し、接合を達成します。そのため、Fig.2からわかるように従来のアーク溶接に比べて溶接速度が大幅に向上するほか、熱影響部が最小限に抑えられ、低熱ひずみや変形のリスクが低減されるため、精密な溶接が実現可能となります。このように溶接プロセスの制御性や加工精度の面で優れている点が大きなメリットです。
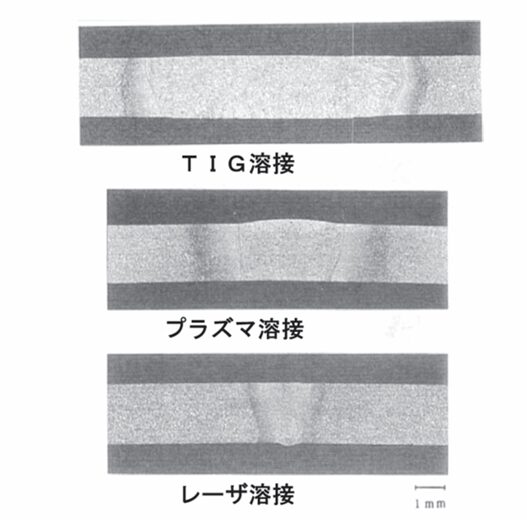
Fig.2 ステンレス鋼薄板のTIG, プラズマおよびレーザー溶接部の断面の比較3
二つ目の特徴は非接触加工であることです。レーザー溶接は加工対象に直接接触することなく加工を実現します。複雑な形状や狭い部位の溶接にも適用可能なため、加工自由度や設計自由度の向上などに効果を発揮します。
レーザー溶接における課題
これまでに説明したように、高速かつ高精度、非接触加工という特徴から、生産性向上に大きく貢献する次世代工法として注目を集めているレーザ溶接プロセスですが、課題も多く存在します。ここでは①プロセス条件の最適化の難しさ、②溶接の良否判定の難しさ、③現象の複雑さと理論モデルの適用の難しさという3つの観点でご紹介します。
① プロセス条件の最適化の難しさ
レーザー溶接の条件設定は、多数のパラメータが複雑に影響し合うため、数多くの試行実験を経た最適化検討が不可欠です。例えば、レーザー出力、ビーム径、溶接速度、ガス流量など各種パラメータについて、綿密な試行錯誤を重ねながら最適な組み合わせを模索していきます。さらに、レーザー溶接プロセスに精通した技術者による解析も必要不可欠な要素です。そのため、プロセス条件の最適化にかかる開発コストの課題は工法としての導入障壁にもなっています。また、近年は製品に使用される部材を適材適所で組み合わせるマルチマテリアル化に伴い、異材溶接の適用検討も増加しています。これは従来以上に複雑な条件設定が必要となり、技術的なハードルが一層高まっています。
② 溶接の良否判定の難しさ
溶接工程一般において最終的に考慮すべき特性は、強度以外にも電気伝導度やプロセス中の熱影響による物性変化など目的によって様々です。さらに評価対象となる項目に分けていくと、溶接部の表面形状や寸法精度など外観検査によってわかるものの他に、溶け込み深さや内部の気孔、微細亀裂など内部状態の正確な評価を要するものもあり、溶接プロセスの良否判定を困難にしています。また、レーザー溶接においてはスパッタの発生も良否の判断において重要な要素であり、数十~数百ミリ秒の加工現象から判定に必要な情報を抽出する技術が求められます。加えて、溶接構造や材質の多様化により多層や非定型の形状の溶接検討を行うことで、溶接欠陥のパターンも複雑化しています。
③ 現象の複雑さと理論モデルの適用の難しさ
レーザー溶接における金属の加工プロセスは、Fig.3のような昇温、溶融、凝固、対流、蒸発などの現象が、マイクロ~ミリ秒単位の非常に短い時間スケールで連鎖的かつ同時に発生します。そのため、全体像を正確に再現するモデルの構築は困難であり、シミュレーションにおける大きな課題となっています。したがって、目的の溶接性能を実現するための溶接条件の予測は困難であり、溶接条件の設定には高度な技術と作業者の経験やノウハウが必要とされてきました。
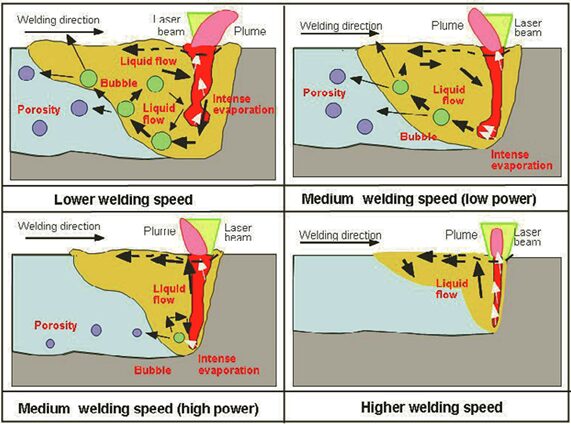
Fig.3 いくつかのレーザー溶接条件における溶融池内現象の概略図4
レーザー溶接プロセスにおける最適化事例
上記のように様々な課題に対し、AIと機械学習の技術を製造プロセスに適用するという新たなアプローチを導入することで、これらのプロセスの効率化と品質向上が期待されています。ここでは、前章でご説明したレーザー溶接プロセスにおける課題①~③に対する最適化事例をご紹介いたします。
機械学習を用いた加工パラメータの最適化
Menoldら5はレーザー加工における複雑なパラメータ空間の課題を解決するため、ベイズ最適化を応用した新たな最適化手法を開発し、レーザー溶接だけでなく、レーザー切断、レーザー研磨といった多岐にわたるプロセスで優れた性能を実現しました。従来、加工パラメータの最適化は多次元の実験計画法や経験に依存しており、試行錯誤によるコストや時間が大きな課題でしたが、著者らは事前知識が限定的な状況下でも、本手法の適用により数十回の実験で十分な最適解を導出できることを示しています。これにより、レーザー加工プロセスの品質向上と生産性の向上が期待され、Industry 4.0時代の製造現場における革新的な改善手法としてさらなる応用が期待されています。
加工状態のリアルタイムモニタリングと良否判定
レーザー溶接プロセスの最適化に向けた取り組みとして、加工状態のリアルタイムモニタリングと良否判定の技術が注目されています。
中島ら6は、車載インバーターの製造プロセスにおけるレーザー溶接のインライン品質保証技術を開発しました。この技術では、溶接時に発生するプラズマ光の波形を統計的手法(重回帰分析など)によって解析し、溶接面積をリアルタイムに推定・監視することが可能となっています。これにより、溶接後に行っていた破壊検査や外観検査に依存せず、製品ごとの溶接品質をその場で評価できるため、工程全体の生産性向上や不良リスクの低減が期待されています。
また、森ら7は、自動車用亜鉛めっき鋼板の重ね溶接を例に機械学習を活用したレーザー溶接のモニタリング技術を開発しました。具体的には、溶融池や金属プルームからの発光強度波形を収集し、それらをニューラルネットワークによって学習させることで、わずかな異常や欠陥の兆候を高精度に検知できます。このように機械学習を組み込んだリアルタイム監視技術を導入することで、幅広い溶接条件の変動にも対応しやすくなり、さらなる溶接品質の安定化や自動化が期待されています。
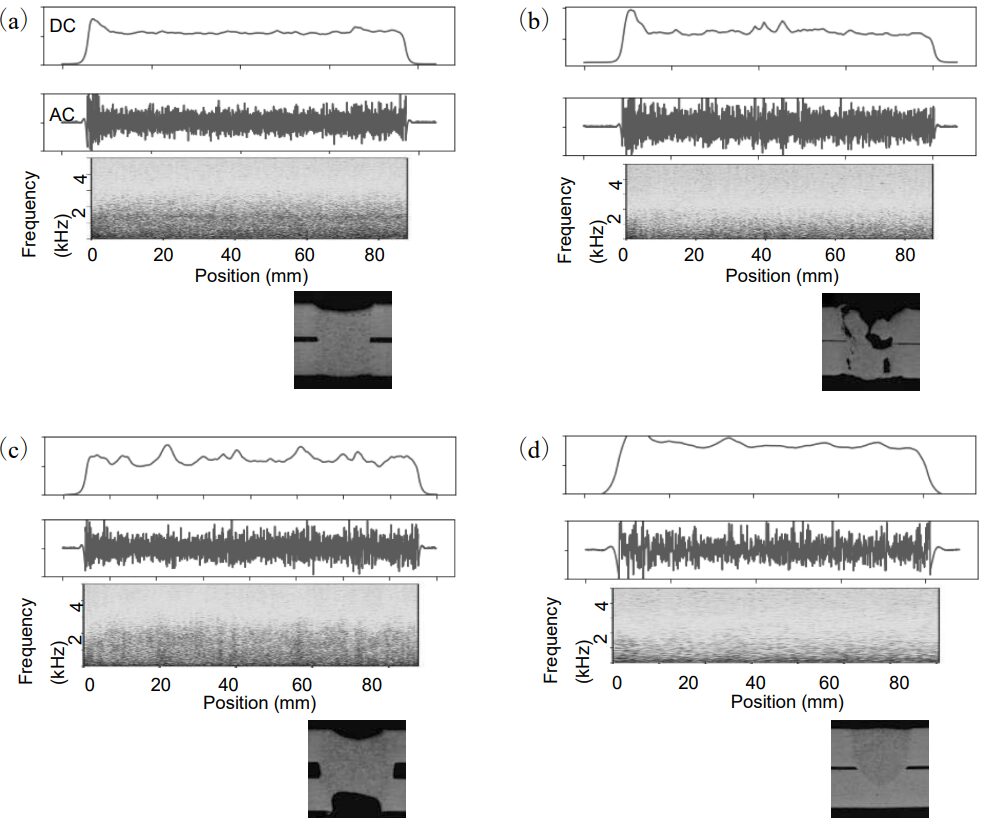
Fig.4 亜鉛メッキ鋼の突き合わせレーザー溶接におけるさまざまな品質波形特性[7]
レーザー溶接シミュレーションの開発とデジタルツイン構築
前章で説明したように、その現象の複雑さゆえに困難とされてきたレーザー溶接プロセスのシミュレーションモデルの構築ですが、研究開発も盛んにおこなわれています。Murua8らはレーザー溶接プロセスに適応したローカルモデル(LM)とグローバルモデル(GM)を組み合わせたマルチスケール数値モデルを開発しました。このシミュレーションモデルによって高い精度での溶接深さや幅などの予測の実現が報告されています。
さらに、坂井ら9は、レーザー溶接プロセスに関するデジタルツインを構築し、AIモデルと組み合わせた自動溶接装置の開発を進めています。このシステムでは、溶融池などの複雑な物理現象をシミュレーションモデルとしてサイバー空間に再現するとともに、加工点の観察を行うモニタリングシステムを実際の実験設備に実装し、AIモデルによってリアルタイムに溶接状態を判定する仕組みを検討しています。
このように、実際のレーザー溶接プロセスとシミュレーションモデル、そしてAIモデルを組み合わせることで、工法開発のさらなる効率化、高度化が期待されています。
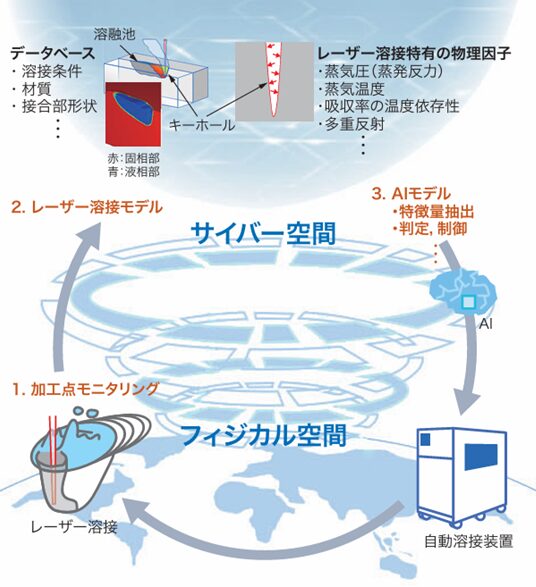
Fig.5 デジタルツインにAIを搭載したレーザー溶接自動システムの概念図[9]
レーザー加工とプロセスインフォマティクスの将来
プロセスインフォマティクスがレーザー溶接プロセスにどんな変化をもたらすのか、今後の展望について考えていきます。
プロセスインフォマティクスとは?
プロセスインフォマティクスは、製造プロセスに関するデータを解析し最適化を行う技術です。データに基づいて製造プロセスを管理することで、品質向上やコスト削減が可能となり、製造業全体の効率化を支えています。
プロセスインフォマティクスについては本テックブログにてとても詳しく解説しておりますので、ご覧ください。
レーザー加工とプロセスインフォマティクス
現状のレーザー加工技術は、材料の違いや複雑な形状、加工条件の多様化など多くの要因が絡み合うため、上記のようにプロセス最適化が難しく、作業者の高度な技術が求められます。一方で、各種センサーとの親和性の高いレーザー加工技術は、プロセスインフォマティクスの活用がさらに進んでいくことで、このような課題を克服できると期待されています。こうした新たなアプローチが、精度や安定性の高さに強みを持つレーザー加工技術の普及と、製造現場のさらなる発展を後押ししていくでしょう。
アイクリスタルはプロセスインフォマティクスのプロフェッショナル集団です。当社の技術やソリューションに関心をお持ちの方は、ぜひ当社のホームページで詳細をご確認ください。
製造業におけるPIの最適なパートナーとして、皆様のご期待に応えます。
お問い合わせはこちら:お問い合わせフォーム
お気軽にご連絡ください。
参考文献
- レーザ加工学会|レーザAtoZ, http://www.jlps.gr.jp/laser/atoz/2/#000151 ↩︎
- 加工用レーザーの種類と特性 | オプティペディア – Produced by 光響, https://optipedia.info/app/laserproc/laser-for-work/ ↩︎
- 片山聖二, “溶接接合教室―基礎を学ぶ― 1-4 レーザ溶接”, 溶接学会誌 第78巻第2号 2009. ↩︎
- Seiji Katayama, Yousuke Kawahito, Masami Mizutani, “Elucidation of laser welding phenomena and factors affecting weld penetration and welding defects”, Physics Procedia 5 9-17 2010 ↩︎
- Tobias Menold, Volkher Onuseit, Matthias Buser, Michael Haas, Nico Bär, Andreas Michalowski, “Laser material processing optimization using bayesian optimization: a generic tool”, Light: Advanced Manufacturing 5:32 2024 ↩︎
- 中島佐知子, 落合大, 福西篤志, “統計的手法を用いたリモートレーザ溶接のインライン品質保証技術の開発”, 自動車技術会論文集 Vol.47 No.2 2016 ↩︎
- 森清和, 石川毅, 薩田寿隆, 奥田誠, 福山遼, 中村紀夫, “機械学習によるレーザ溶接モニタリング技術”, レーザ加工学会誌 Vol. 28, No.2 2021 ↩︎
- O. Murua, J.I. Arrizubieta, A. Lamikiz, H.I. Schneider, “Numerical simulation of a laser beam welding process: From a thermomechanical model to the experimental inspection and validation”, Thermal Science and Engineering Progress 55 2024 ↩︎
- 坂井哲男, “レーザー溶接のCPS化による製造プロセスの自動化”, 東芝レビュー Vol.74 No.5 2019 ↩︎