鉄鋼分野における熱処理技術は、長きにわたる歴史を通じてその重要性を高めてきました。紀元前のアナトリア半島における鉄器製造から始まり、熱処理は丈夫な武器や農具を製造するための不可欠な技術として発展します。産業革命を経て鉄鋼の用途は大きく広がり、簡単な道具としてだけでなく、例えば建築部材や鉄道・自動車などのインフラストラクチャ、機械部品へと多岐に渡る用途で利用されるようになり、その過程で求められる機能も高度化してきました。それを受け、錆びない材料としてステンレス鋼、ワイヤーなど引張強度に強い材料のピアノ線材、工具としてとにかく硬くあって欲しい工具鋼、バランスの良い強度と靭性が求められる機械構造用鋼、様々な用途に応じて多様な熱処理技術が生み出されてきました。
現代においても熱処理技術の進化は留まることなく、世界中の技術者たちは絶えず技術を磨き合い、常に新たな高みを目指し競い合っています。そして近年、製造業界ではデジタルトランスフォーメーション(DX)の波が押し寄せ、コンピュータ技術の進化がその潮流を一層加速させています。特にAIの活用が普及し始め、従来の「カン・コツ・経験」に基づく研究開発に革命をもたらしています。職人やエンジニアたちはAIを新たなツールとして取り入れ、伝統と最新技術を融合させた新たな研究開発手法を模索しています。
本記事では、熱処理技術の基礎と課題、さらに AIを活用した熱処理プロセス最適化、いわゆるプロセスインフォマティクス(PI)について、具体的な事例を交えて解説します。
鋼材における熱処理の再確認 | 目的と分類
鉄鋼材料の熱処理は、基本的でありながら最も重要なプロセスの一つです。
熱処理とは
鉄を溶かしてそのまま固めたものを鋳鉄と呼び、高い硬度を持っているものの、そのままでは非常に脆く衝撃に弱いため構造材として使用するには適していません。また鋳鉄は加工が難しく、用途に応じた特性を持たせるのも容易ではありません。そこで鉄鋼材料として実用的な形に変えるために行われるのが、鍛造と熱処理です。鍛造では、鋳鉄に力を加えて形を整え組織内部に転位を導入することで、その強度と靭性を高めます。しかし、まだこれだけでは十分ではなく、さらに熱処理が必要です。熱処理は、鉄鋼材料の性質を大幅に改善し、用途に応じた特性を付与するための重要な手段です。熱処理により、鉄鋼材料はより実用的なものへと生まれ変わります。熱処理は鉄鋼材料の性能を最大限に引き出し、幅広い用途に適応させるために欠かせない工程です。
4種類の熱処理
熱処理には様々な手法がありますが、ここでは焼き入れ、焼き戻し、焼きなまし、焼きならしの四つについて解説します。
1. 焼き入れ
炭素鋼は高温において面心立方格子であるオーステナイトの状態を呈し、低温においては体心立方格子であるフェライトの状態を呈します。図1が示すように、平衡状態に近い徐冷をすると、変態開始線と変態終了線の間で変態が進行します1。オーステナイトは多くの炭素を固溶できますが、フェライトは炭素をほとんど固溶できません。オーステナイトはフェライトに変態する際、フェライトが固溶しきれない分の炭素を周囲に排斥します。これにより、フェライトの周囲では炭素濃度が高くなります。炭素濃度が高くなった部分では鉄と炭素が結合し、セメンタイトが形成されます。その時、セメンタイトは多くの炭素を必要とするため周囲から炭素を集め、結果としてセメンタイトの周囲では炭素が少なくなります。そうなると、今度は変態前の組織であるオーステナイトから炭素が排斥されながらフェライトが生じます。このようにして、フェライトとセメンタイトが交互に重なる組織が現れます。これをパーライトと呼びます。上記の通り、高温の炭素鋼を徐冷するとパーライトやフェライトが分布した組織になりますが、非常に速く冷却をすると炭素が拡散する前に組織が変態し、炭素を無理に固溶した体心正方格子が生じます。これをマルテンサイト組織と言います。マルテンサイトは、本来固溶できるはずのない量の炭素を固溶するため大きな歪みが発生し、その歪みが焼き入れにより得られる高強度の要因となります。
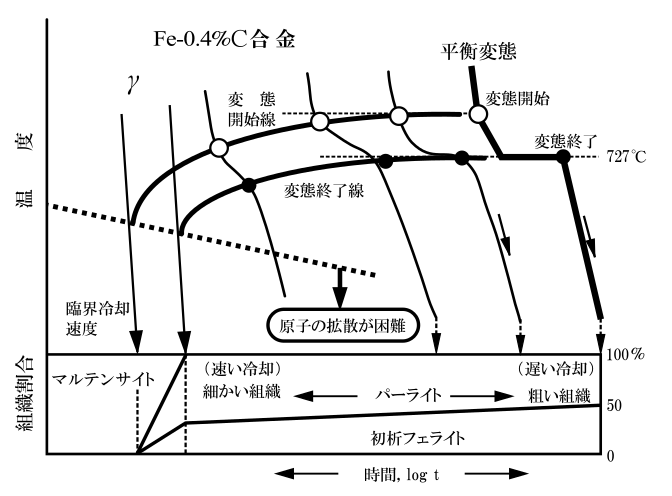
2. 焼き戻し
焼き入れによって得られるマルテンサイト鋼は、強度は高いものの非常に脆くなっています。この脆さを改善し、粘りを出すために行われるのが焼き戻しです。焼き入れした材料を一定の温度まで加熱すると炭素の移動が可能になります。マルテンサイトに無理に固溶していた炭素が拡散し、マルテンサイトは低炭素マルテンサイトに、拡散した炭素は周囲の鉄と化合物を作りセメンタイトになります。焼き入れにより生じた大きな歪みが解放され、材料の脆さが低減します。
3. 焼きなまし
炭素鋼の強度を上げる方法の一つに加工があり、これにより結晶粒内の転位密度が増加します。転位密度が増加すると、転位の移動は転位同士の相互作用によって妨げられ、その結果、材料の変形が起こりにくくなります2。 しかし、一般に材料は強度が高くなると脆くなる性質があります。このバランスを取るためには、結晶粒内に生じた転位を解放する必要があります。焼きなましとは、材料を高温に加熱することで結晶粒に導入された転位を解放し、金属原子の再配列を促し、転位のない新しい結晶を生じさせる方法です。再配列の仕方には回復と再結晶とがありますが、どちらも転位を減らす効果があり、脆くなってしまった材料に粘り気を与える効果があります。

4. 焼きならし
熱間圧延の際、ランダムな方位を持つ結晶が一方向に延ばされ、横に伸びたオーステナイトが形成されます。オーステナイト域から徐冷すると、フェライトの形成に寄与する原子が偏析している部分ではフェライトが形成され、そうでない部分には炭素が偏析してパーライトが形成されます。しかし、オーステナイト域から空冷程度のあまり遅くない速度で冷却すると、フェライトとパーライトが均一に混合した正常な組織を得ることができます。これを焼きならしと呼びます。
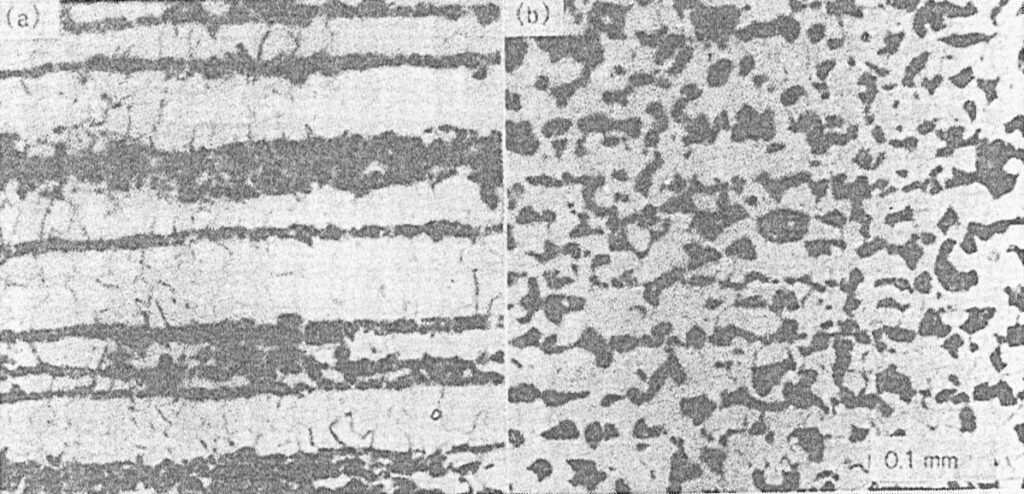
熱処理における諸課題とその原因
熱処理は基本的な技術であり、技術的にも確立していると思われがちですが、環境や熱処理炉の構造、炉体の癖などによって全く違った課題が存在します。またそれだけでなく、昨今のCO2対策など環境問題においても重要な課題を抱えている分野の一つです。
熱処理プロセスの省エネルギー化 | 環境問題への対応
熱処理プロセスには高温が欠かせないため、天然ガス、LPG、重油、石炭などを燃焼させた熱が利用されていますが、世界は脱炭素社会の実現に向けて動き出しており、日本国内の鉄鋼メーカーもこの流れを無視することはできません。カーボンニュートラルを目指す中で、ガス炉から電気炉への転換、および、アンモニアや水素の利用が検討されていますが、これらの取り組みにはそれぞれ課題が存在します。
アンモニアや水素の供給がまだ不安定であること、さらにアンモニアは燃焼の安定性が悪く、水素は水素脆性の問題があります。電気炉では、炉内の均一温度維持や急速加熱が課題とされています。
これらの問題に対処するため、様々なメーカーが積極的に新たなプロセスの開発に取り組んでいます3。
焼き割れ・焼き入れ変形による後工程のコスト
高硬度鋼のように炭素濃度が高く多種の合金元素が添加される材料の場合、その組成が熱処理の挙動に大きく影響します。これらの鋼材は熱伝導率が小さく、熱処理時に鋼材の内側と外側とで大きな温度差が生じ、その結果、熱処理歪みが発生します。この熱処理歪みが焼き入れ変形を引き起こす要因となります。また、これらの鋼材はMs点-Mf点(マルテンサイト変態の開始点と終了点)が比較的低温であり、塑性変形しにくい低温下でマルテンサイト変態を起こすため残留応力が増大し、結果、大きな引っ張り応力が発生することで楔形の焼き割れを生じさせます。このような焼き入れ変形や焼き割れが発生すると、後工程での修正や矯正のコストが大きく増加します。
合金元素の組成を変更して問題に対処することも可能ですが、組成に厳しい要求仕様がある場合は熱処理プロセスの最適化が必要です。一般的に熱処理歪みによる焼き入れ変形や焼き割れに対しては、熱処理中に鋼材の内側の温度と外側の温度とが均一になるよう保つように調整が行われ、マルテンサイト変態による焼き入れ変形や焼き割れに対してはマルテンサイト変態領域での塩浴焼き入れや引き上げ焼き入れによる徐冷が行われます。
しかし、いずれの場合でも非常に難しい微妙な調整が必要とされます。
熱処理プロセスの熟練技術者への依存
熱処理技術は長い歴史を持ち、その手法は極限まで磨かれてきました。伝統的な方法は今もなお広く用いられており「JIS G0566 鋼の火花試験方法」のような標準化された手法が確立されています。そのため、センシング技術が進展しているにも関わらず、熟練技術者の目で見たり、耳で聞いたりする判断が重要である場合が多いです。これは、センサーで状態を定量化する際に、様々な情報が失われることが一因です。
一方で、熟練技術者の減少と技術習得の長期化とが業界の大きな課題です。すべてをAIに置き換えることは困難であり、人の感覚や経験に依存する部分が依然として大きいですが、技術の言語化が難しい部分をAIに置き換えることが求められており、熟練技術者の技術をAIに学習させる試みが行われています。
熱処理プロセスにおけるAI活用事例
熟練技術者の手によって行われている熱処理、そのプロセスも一部AIを活用して省エネルギー、省コストを実現することが可能になってきています。AIによって熟練技術者の貴重な時間を解放し、より重要なプロセスのみに集中することで製品の品質向上を期待できます。
製造プロセスにおけるAIの定義と機械学習
熱処理プロセスは鉄鋼分野において非常に重要な工程であり、精密な制御によって成り立っています。一方で、誘導加熱によるランダムな加熱ムラが発生したり、熟練技術者の目視によって温度を見極める属人的な管理がされていたりと、不安定な部分も多く存在します。さらに断熱材やローラーなど炉内の部材の劣化、季節や風向きによる炉内の温度分布の偏りなど、監視をすることができても管理をすることが難しいものもあるなど、これら様々な要因を常に最適な状態に保つことが求められます。しかし、これらの複雑なプロセス管理も、機械学習の技術を活用することで解決できる場合が増えてきています。機械学習を用いることで、これまで人間の経験と勘に頼っていた部分を、データに基づいた予測と制御に置き換えることが可能となります。例えば、機械学習モデルを用いることで、過去のデータを分析し、温度やガス消費量の最適な設定値を提案することができます。また、異常検知技術を用いれば、炉内の温度分布や断熱材の劣化の兆候を早期に検出し、プロセスの安定性を保つためのメンテナンス計画を立てることも可能です。
機械学習を熱処理プロセスに適用するには、まず温度や時間、ガス消費量などのデータを収集し、ノイズ除去や正規化を行うことが重要です。次に、収集したデータを基に回帰分析や分類などの手法で機械学習モデルを構築します。このモデルを用いてプロセスを最適化することで、製造の効率化や品質向上が期待できます。例えば、観測データに基づいて精度の高い予測を行い、新たな条件下での結果を迅速に得ることが可能です。
このように、機械学習の技術を適用することで、熱処理プロセスの効率化と安定化を図ることができます。今後、さらに高度な技術が開発されることで、より精密で効率的なプロセス管理が可能になるでしょう。
ディープラーニングによる金属組織の認識
金属材料は同じ組成であっても、その加工や熱処理によって強度や耐食性が大きく変化します。金属組織の観察は、こうした変化を把握し、熱処理の適切さや材料の強度を推定するために非常に重要な技術です。
これまで、金属組織の判定は専門家が経験に基づいて行ってきました。しかし、この方法ではどうしても属人化してしまい、さらに判定者によって結果が異なることもしばしば起こります。そこで、客観的かつ安定した判定が求められ、その手段としてディープラーニングが注目されています。
新潟県工業技術総合研究所 中越技術支援センター では、実際に焼入れ温度が異なる鋼材の金属組織をディープラーニングによって認識させ、高い正解率で金属組織を判別できたという成果を得られています。焼入れ温度が高すぎると金属組織が粗くなり、結果として材料がもろくなることが知られています。このため、金属組織が粗いかどうかを判別できれば、焼入れ温度が適正であったかどうか、材料のもろさを判断することが可能になります。
機械構造用炭素鋼S50Cを850℃、950℃、1050℃、1150℃の各温度で10分間保持し、水冷焼入れを行いました。試料の端面を鏡面研磨し、ナイタールによる腐食処理を行った後、図4のように金属組織の写真を撮影しました。これらの画像をVGG16という学習済みのディープラーニングモデルに学習させたところ、約50回の学習で90%の正解率を達成しましたが、それ以上は精度が向上しませんでした。それでも、人間では見分けが難しい組織を正解率9割で認識できたことは、非常に有望な成果と言えるでしょう4。
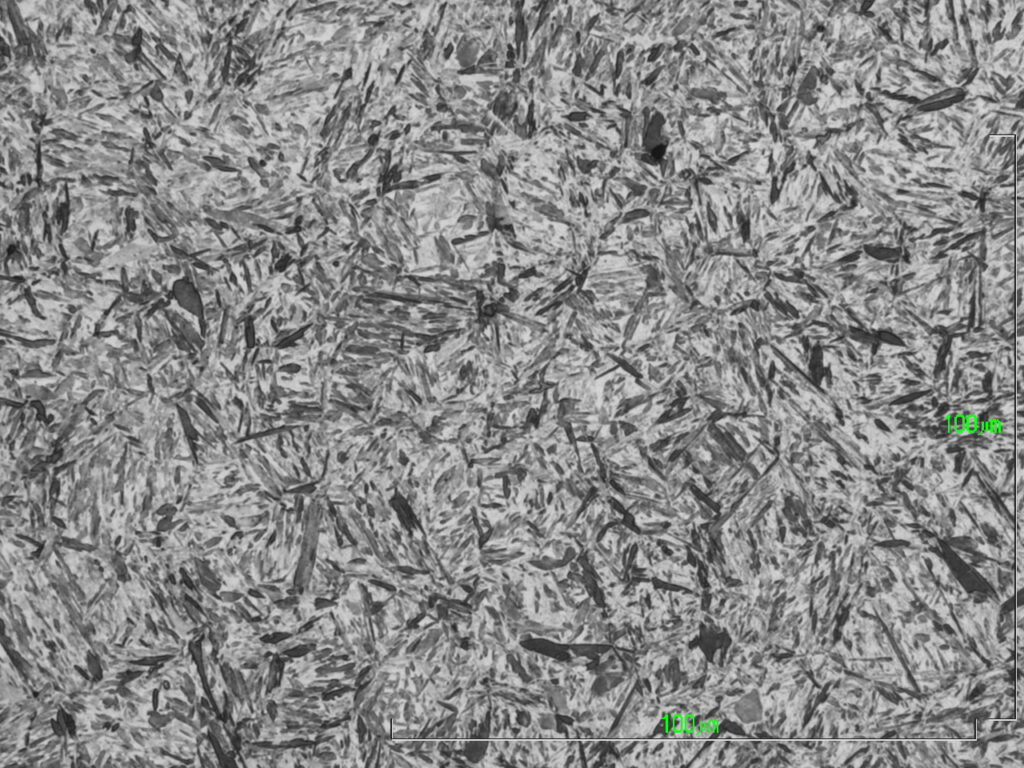
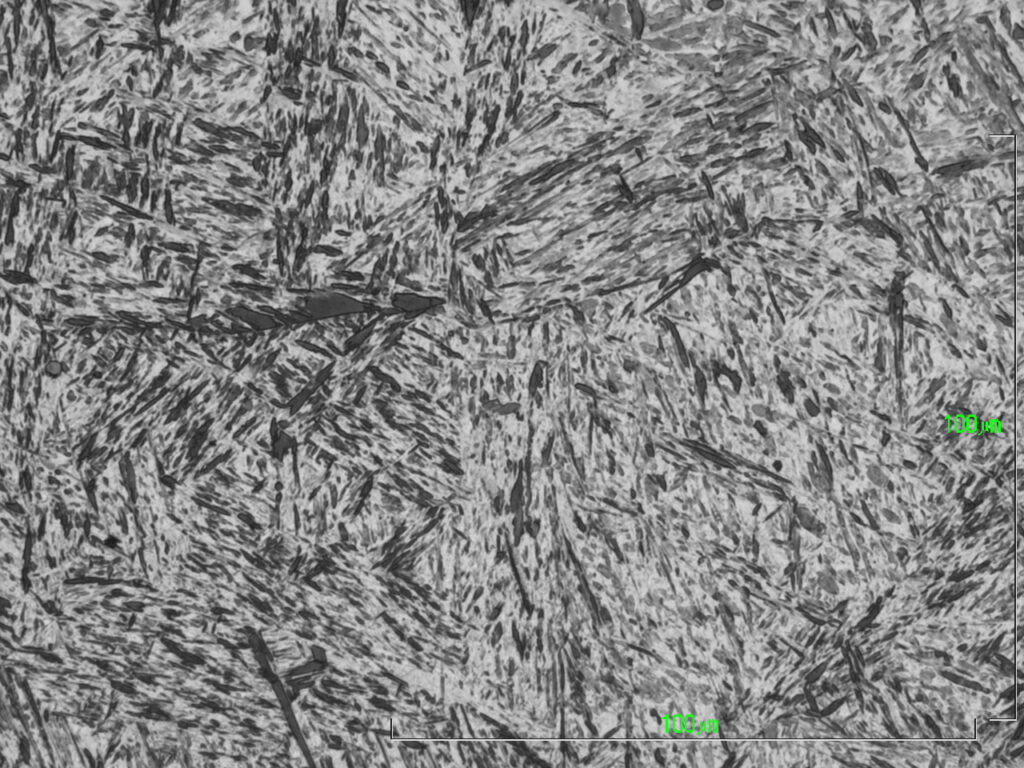
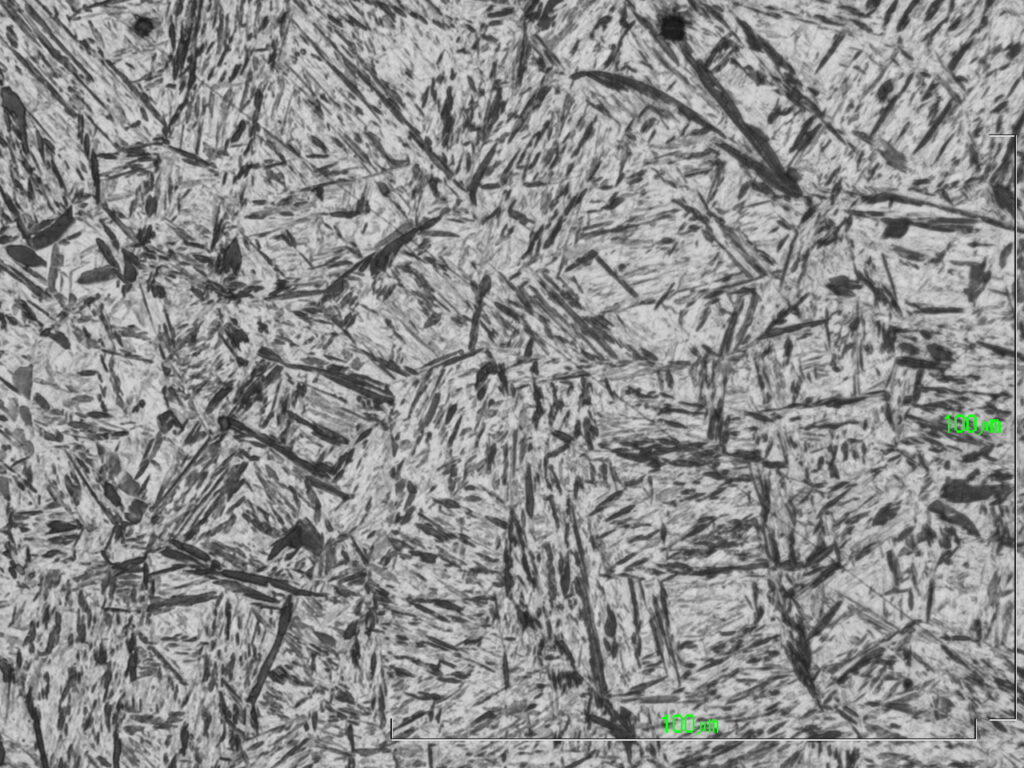
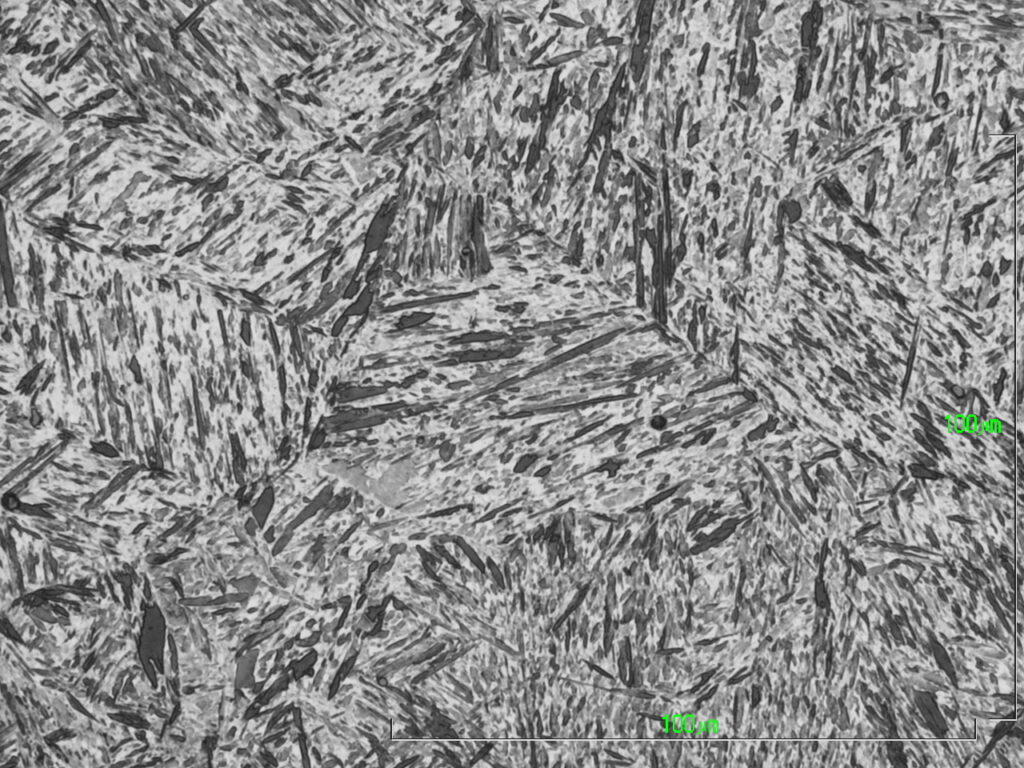
図4 各焼き入れ温度による組織写真[4]
熱処理装置の異常予兆の検知
産業機器の運用において、従来の異常検知はしきい値ベースで行われていましたが、そこには限界があり現在では機械学習によりセンサー信号の相関関係や時間軸を考慮した分析が可能になってきました。これにより、産業機器の運用における安全性と効率が向上すると期待されます。
熱処理装置においても従来の手法では対応が難しい劣化や異常の早期発見が求められています。例えば、高い疲労強度や耐摩耗性を求められる材料には浸炭処理が施されますが、この処理を行う炉の内部環境は非常に過酷で、炉体の部材に異常が発生しても検知が遅れることがあります。結果、炉体の部材が重大な破損を招くことになり、生産計画に大きな支障をきたすリスクが存在します。
株式会社ジェイテクトでは、データマイニング技術の研究とクラウドを用いたデータ収集・分析プラットフォームの開発を進めており、実際の機械を用いたシステムの実証試験に取り組んでいます。具体的な例として、に示すバッチ式浸炭炉では搬送系のトレイプッシャーが日々の運転で徐々に劣化していくことがあり、その進行を見逃さないための仕組みが必要です。
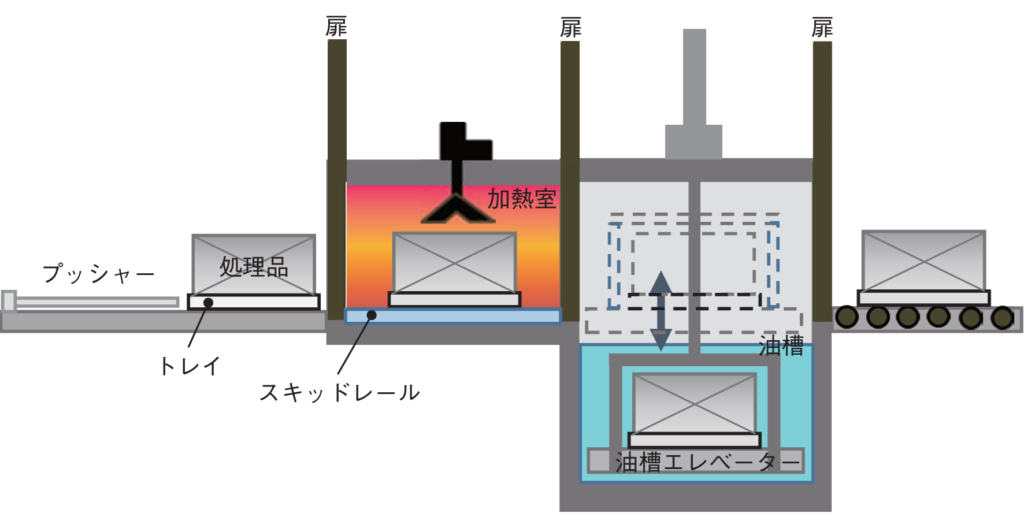
トレイプッシャーは、処理品を載せたトレイを金属ロッドで押し、スキッドレール上を移動させる装置です。バッチごとに処理品の重さや形状が異なるため、搬送力のプロファイルが変動し、そのため劣化診断が難しいとされています。この問題を解決するために、搬送力のプロファイルから特徴量を抽出し、機械学習を用いて劣化の進行をモデル化しました。スキッドレールのひずみが発見されてから交換までの期間、新品交換後の期間、それぞれのデータをもとに異常スコアを算出、この異常スコアを連続的に追跡することで劣化が進行するタイミングを見極め、適切な交換時期を判断できるようになりました5。
熱処理にも適用できるプロセスインフォマティクス
熱処理プロセスは複雑であり、そうそうAIに置き換えることができないことは事実です。しかし機械学習を用いることで一部の作業は自動化でき、また今まで言語化できなかった判断基準を明確にすることが可能になります。その性質を利用し、熱処理プロセスを最適化することをプロセスインフォマティクス(PI)と言います。プロセスインフォマティクスについては、本テックブログ別記事にてとても詳しく解説しておりますので、ぜひご覧ください。
熱処理のプロセスインフォマティクスの将来性
熱処理のプロセスインフォマティクスは、様々なセンサー等から集めたデータを解析し、プロセスの最適化を進めるアプローチです。エネルギー効率の向上はCO2排出削減や環境負荷の低減を期待でき、また製品コストを下げる効果もあります。さらに技術者の手を作業から解放することによって人的ミスを低減させたり、本来集中すべき作業だけに集中してもらうことによって製品の品質を向上させたりすることにもつながります。熱処理のプロセスインフォマティクスは、持続可能な社会の実現を目指す一歩になることでしょう。
アイクリスタルはプロセスインフォマティクスのプロフェッショナル集団です。当社の技術やソリューションに関心をお持ちの方は、ぜひ当社のホームページで詳細をご確認ください。
製造業におけるPIの最適なパートナーとして、皆様のご期待に応えます。
お問い合わせはこちら:お問い合わせフォーム
お気軽にご連絡ください。
- 高木節雄、津崎兼彰.”マテリアル工学シリーズ2 材料組織学”.株式会社朝倉書店.2001 ↩︎
- 日本金属学会.”講座・現代の金属額 材料編4 鉄鋼材料”. 社団法人日本金属学会.2002. ↩︎
- 経済産業省・製造産業局.”「製造分野における熱プロセスの脱炭素化」プロジェクトの研究開発・社会実装の方向性”.第11回 産業構造審議会 グリーンイノベーションプロジェクト部会 産業構造転換分野ワーキンググループ.2023-02-15.https://www.meti.go.jp/shingikai/sankoshin/green_innovation/industrial_restructuring/pdf/011_03_00.pdf ↩︎
- 新潟県工業技術総合研究所 中越技術支援センター 斎藤雄治.”焼き入れ温度が異なる炭素鋼のディープラーニングによる金属組織の認識”.新潟県工業技術総合研究所.-.http://www.iri.pref.niigata.jp/topics/R2/2kin8.html ↩︎
- 服部 昌、鈴木真之佑.”熱処理装置のIoT -以上の予兆をとらえるデータ分析技術-“.JTEKT ENGINEERING JOURNAL No1018.2021.https://www.jtekt.co.jp/engineering-journal/assets/1018/1018_13.pdf ↩︎