研削加工とは、研削砥石を使って金属やその他の材料を精密に削る加工技術です。この方法は高い精度と仕上げ品質が求められる場合に特に有効で、製造業や機械工業で広く利用されています。研削加工のメリットは、寸法精度と表面仕上げの両方を同時に達成できる点です。しかし、研削加工には工具の摩耗や加工時間の長さといった課題も存在します。これらの課題を解決するために、機械学習を活用してプロセスの最適化が進められています。
本記事では、研削加工の基礎からAIによるプロセスの最適化までを解説し、高度な製造技術と最新の機械学習の応用例を解説します。
研削の基礎知識
研削加工とは? | 研削、切削、研磨の違い
研削加工とは、研削砥石を用いて金属などの材料を精密に削る加工法です。
以下に、研削・切削・研磨の違いを述べていきます。
研削:高速回転する砥石の表面に分布する多数の砥粒によって工作物を微量ずつ削り取って精密に仕上げる加工法
切削:工具を工作物に切り込ませ表面から不要部分を除去し、目的となる寸法・形状を作り出す加工法
研磨:圧力切込み加工により、工作物表面を極微量ずつ除去することで良質な仕上げ面を得る加工法
・4種の代表的な研削加工
研削加工の方法として代表的なものに、平面研削、内面研削、円筒研削、センタレス研削があります。
以下に、上記4つの研削方式の違いを述べます。
・平面研削:
平面研削盤を使用して平らな表面を精密に削る加工法です。主に金属部品の平滑性と寸法精度を高めるために使用され、平行度や直角度などの高い要求を満たすことができます。工具の動きと加工物の動きを組み合わせることで、広い範囲の表面を均一に仕上げることが可能です。
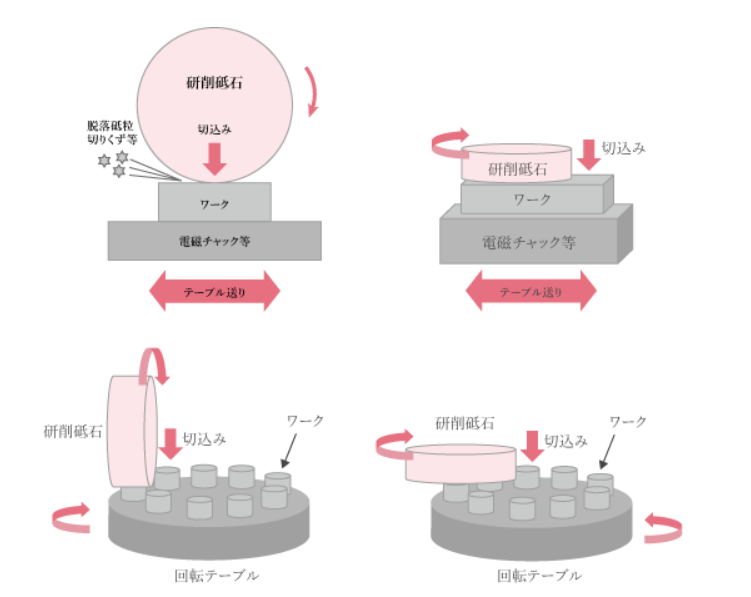
・内面研削:
内面研削盤を用いて部品の内径や穴の内側を高精度に削る加工法です。特に、ベアリングやシリンダーなどの部品の内面仕上げに特化しており、内径の寸法精度や表面の滑らかさを向上させることができます。工具の直径が小さく、複雑な形状の内面にも対応可能です。
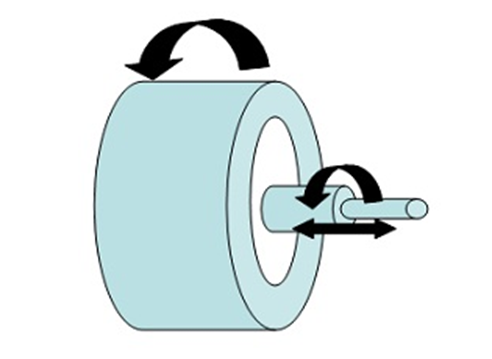
・円筒研削:
円筒研削盤で円筒状の外径を精密に削る加工法です。軸やロールなどの回転対称な部品の外周を高精度に仕上げる際に使用されます。加工物を回転させながら、研削砥石で削ることで、均一な外径寸法と滑らかな表面を実現します。長尺物や大径物の加工にも適しています。
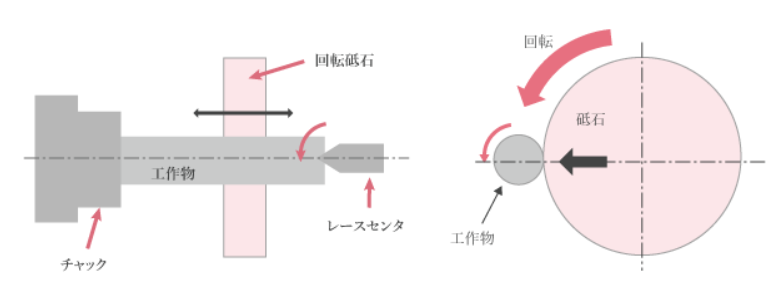
・センタレス研削:
工作物を固定せず、円筒状の部品を支持しながら削る加工法です。高速かつ連続的な加工が可能で、量産品の加工に適しています。支持具と調整砥石の間に工作物を配置し、回転させながら研削することで、高精度かつ効率的な加工が可能です。・センタレス研削:
工作物を固定せず、円筒状の部品を支持しながら削る加工法です。高速かつ連続的な加工が可能で、量産品の加工に適しています。支持具と調整砥石の間に工作物を配置し、回転させながら研削することで、高精度かつ効率的な加工が可能です。
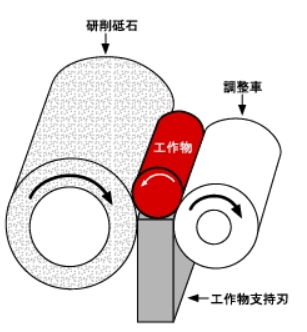
研削加工の課題 | 品質と生産性の向上を同時に達成するために
研削加工における技術継承や難削材対応など、品質と生産性を両立するための課題と従来の課題解決方法を解説します。
熟練研削技術者の技術継承
研削加工が熟練技術者に依存する理由は、複数の要素が高度に関連し合うためです。特に、被削材だけでなく、砥石自体も精密に加工する必要があることから、経験豊富な技術者の判断が求められます。これに対し、現在の課題解決方法としては、加工システムの最適化や自動化技術の導入が挙げられます。特に、加工工程の一部を自動化し、機上計測を活用することで、熟練技術者の技術を他の作業者でも再現可能にする取り組みが進められています。
難削材の高品質研削と砥石設計
難削材の加工は、従来から多くの課題を抱えてきました。例えば、ステンレスやチタンといった高硬度材料は、加工時の高熱が逃げにくく、工具の摩耗や加工精度の低下を引き起こすため、工具交換の頻度が増えることでコストが上昇します。このような課題に対して、高性能の切削工具や冷却剤の導入が試みられてきました。また、新素材を加工する際には、メーカーが提供する加工データや類似の経験が乏しいこともあるため、試行錯誤しながら加工条件を探索します。これらの方法で一定の改善は見られるものの、依然として加工費は高く、技術革新が求められています。
研削焼けによる悪影響
研削加工において、砥石の劣化は研削焼けを引き起こし、加工精度や製品の品質に直接的な悪影響を与えます。研削焼けは、材料の表面に過度な熱が加わることで硬化層やクラックが発生し、最終製品の性能や耐久性を損ないます。これを防ぐためには、砥石の適切な管理や定期的な交換が不可欠ですが、その交換にはコストがかかり、生産効率の低下も避けられません。現在、砥石の劣化を早期に検知し、最適なタイミングで交換する技術や、研削条件をデータ分析に基づいて最適化する取り組みが進んでいます。
研削のインフォマティクス活用 | 既存の製造装置の最適化
研削加工の課題は、機械学習やAIを活用したデータ解析により、加工条件の最適化が可能となり解決が進んでいます。
機械学習とは? | 研削プロセスとの関係とは
機械学習とは、大量のデータを基にパターンや傾向を見つけ出し、そこから予測や判断を自動で行う技術です。研削加工では、砥石の摩耗や加工速度、加工対象の品質など多くの要因が絡み合う複雑なプロセスが含まれます。従来の手法では、これらの要因を個別に解析し、経験や勘に頼った判断が主でした。しかし、機械学習を活用することで、これまで蓄積された加工データを解析し、最適な加工条件や異常の兆候を自動で検出・予測することが可能です。プロセスインフォマティクスは、データを駆使して製造プロセス全体の効率を向上させるための手段であり、次節以降で各社の事例を参考にしながら具体的な事例を理解しやすくするために解説していきます。
リアルタイムデータ解析による適切な研削条件の発見
リアルタイムデータ解析を用いた研削条件の最適化は、研削加工の効率と品質向上において大きな進歩を遂げています。Surindraらの研究では、機械学習モデルを活用して研削ベルトの摩耗状態をリアルタイムで監視し、予測精度を向上させる取り組みを実施しました5。具体的には、センサーデータを用いて振動や力の変動を解析し、k近傍法やサポートベクターマシン、決定木、ランダムフォレストなどのアルゴリズムを比較検討しました。その結果、決定木とランダムフォレストが最も高い精度と低遅延を示し、効率的な研削条件の発見が可能となり、製造プロセス全体のコスト削減にも寄与しています。この技術により、従来の手作業に依存しない高度な自動化が実現され、将来的にはIoTを活用したリアルタイムモニタリングシステムへと発展が期待されています。
ベイズ最適化を用いた研削条件の最適化
ベイズ最適化は、限られたデータで効率的に最適な条件を見つけるための手法です。特に、試行錯誤にコストがかかるような研削加工の条件最適化に非常に適しています。
- ベイズ最適化とは?
ベイズ最適化は、機械学習の一種で、不確実な状況で最適な結果を見つけ出すための手法です。従来の最適化手法は、多くのデータや試行を必要とすることが多いですが、ベイズ最適化は少ないデータからでも効率的に次に試すべき条件を提案してくれます。これは、実験や試行に時間やコストがかかる場面で特に役立ちます。
一方、類似の手法として実験計画法(DOE)というものがあります。DOEは、要因が結果に与える影響を評価するための体系的な方法です。複数の要因を組み合わせて実験し、どの要因が結果に最も寄与しているかを明らかにします。DOEは要因の主効果や交互作用を解析するのに効果的です。
研削のように実験コストや時間が多くかかってしまうプロセスには、限られた試行回数の中で最適解に到達することを目指すベイズ最適化の方が適していると言えます。
- ベイズ最適化の仕組み
ベイズ最適化の特徴は、「事前確率」と「事後確率」という考え方に基づいています。最初に、条件や結果についての初期的な予測(事前確率)を設定します。その後、実際に実験や試行を行い、新たなデータを得ます。このデータを基に、予測を更新していきます。これを繰り返すことで、徐々に最適な条件に近づいていくのです。
特に研削加工においては、砥石の摩耗や温度、加工時間など、あらゆるデータを基にしたベイズ最適化が、最小限の試行で最適な条件を見つけ出し、加工効率や品質を大幅に向上させます。
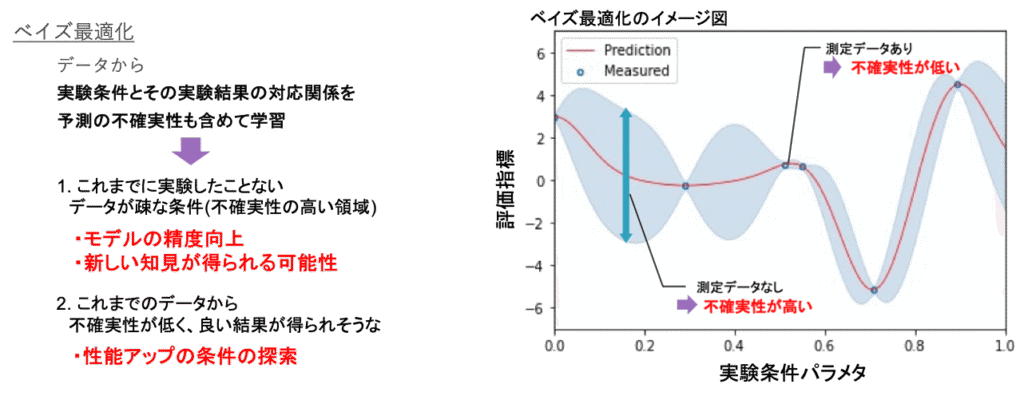
- 研削条件の最適化との関係
研削加工では、砥石の種類、回転速度、送り速度、ウェハの回転速度など、多くのパラメータが関係し、それぞれが加工精度や品質に大きな影響を与えます。小泉らの研究では、全ての組み合わせを試して最適な条件を見つけるのではなく、ベイズ最適を用いて少ない試行から効果的に条件を絞り込み、最適な加工条件を効率的に見つけることに成功しました6。
- まとめ
ベイズ最適化は、データが少ない状況や試行錯誤のコストが高い場合に、最適な条件を効果的に見つける手法です。研削加工においても、この手法を活用することで、品質向上とコスト削減が同時に実現可能となり、現場でのデータ活用が進む中で、今後さらに重要性が増していくと期待されています。
知識のデジタル化による研削条件決定システム
磯村らは、熟練者の暗黙知や形式知をデジタル化し、研削加工の最適な条件を自動で提案するシステムを構築しています7。この技術は、熟練者の思考過程を因子間のネットワークで表現し、そのつながりをデータで可視化することで、誰でも精度の高い加工が可能となります。特に、TAKUMI NEURONというシステムでは、入力された工作物や砥石の情報を基に、最適な回転速度や送り速度を算出し、加工精度や砥石寿命を予測します。このシステムは、研削条件の検討時間を短縮し、試行錯誤のコストを削減することができ、熟練者と同等の精度を実現するための重要なツールとなっています。
まとめ:研削加工のプロセスインフォマティクスの将来性
いかがでしたでしょうか。研削加工におけるプロセスインフォマティクスは、精度と効率を両立させる未来の鍵です。
研削にも適用可能なプロセスインフォマティクス
研削加工における課題は、熟練者の技術に依存する点や、最適な加工条件の設定が難しい点です。これに対し、プロセスインフォマティクスの適用により、データ解析を活用して加工条件の最適化が可能となり、生産性と品質の両立が実現します。リアルタイムのデータ収集と機械学習を組み合わせることで、異常の検出や最適条件の自動提案が行えます。将来的には、より多くの加工プロセスにこの技術が適用され、効率化がさらに進むことが期待されます。
- 平面研削盤とは?平面研削機の種類と仕組みを知って加工にいかそう -さくさくEC, https://sakusakuec.com/shop/pg/1plane/ ↩︎
- 内面研削盤の特徴と利点 -株式会社酒井鉄工所, https://sakaitec.co.jp/engineering/machinetool/334 ↩︎
- 円筒研削盤とは? センタレス研削/研磨との違いを知って加工に生かそう -さくさくEC, https://sakusakuec.com/shop/pg/1cylinder/ ↩︎
- センターレス研削(心なし)研削 -東大阪市技術交流プラザ, https://www.techplaza.city.higashiosaka.osaka.jp/help/word/grinding/centerless_grinding.html ↩︎
- Use of machine learning models in condition monitoring of abrasive belt in robotic arm grinding process, Mochamad Denny Surindra、Gusti Ahmad Fanshuri Alfarisy、Wahyu Caesarendra、Mohamad Iskandar Petra、Totok Prasetyo、Tegoeh Tjahjowidodo、Grzegorz M. Królczyk、Adam Glowacz、Munish Kumar Gupta, Journal of Intelligent Manufacturing(2024),https://link.springer.com/content/pdf/10.1007/s10845-024-02410-6.pdf ↩︎
- 機械学習による検索条件の最適化Ⅱ, 小泉晴比古、花田賢志、金子弦、原田俊太、成田潔、宇治原徹,あいちシンクロトロン光センター 成果報告書(2018),https://www.aichisr.jp/content/files/seikahoukoku/2018/8S2_2018a0026.pdf ↩︎
- 知識のデジタルモデル化技術を用いた検索条件決定システムの開発,磯村 秀和、小島 大,JTEKT ENGINEERING JOURNAL No.1018(2021), https://www.jtekt.co.jp/engineering-journal/assets/1018/1018_11.pdf ↩︎